冲压工艺可制备多种规格的薄壁零件,故利用冲压制备镁合金 3C 产品的工艺将极具吸引力和市场价值,故提高镁合金板材的冲压成形性能,对镁合金板材的冲压成形工艺的研究是非常必要的。目前,已经研发出的冲压成形技术主要有:局部加热、无模分层成形技术、多点成形工艺、变压边力技术、叠层拉深工艺、激光成形技术、差温拉深技术、气压胀形及液压胀形、超塑性成形、成形过程的计算机仿真技术、冲压智能化技术、粘介质成形技术等。大量研究表明,选择合理的冲压工艺参数是实现板材冲压成形的必要条件,影响板材冲压成形性能的工艺参数主要包括成形速度、模具结构、润滑条件、压边力、成形温度等。
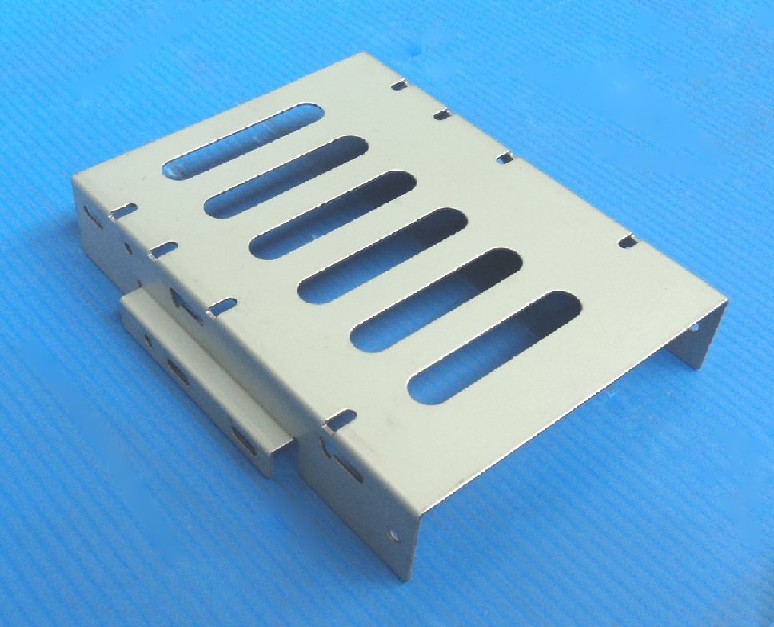
(1)成形速度 镁合金板材是应变速率敏感材料,其成形能力受成形速度的影响较大。有关研究表明,当拉深速度为 7 .5mm /min和 30mm /min时,镁合金板材可以制得拉深比达 2.65 的圆筒形拉深件,而当拉深速度提高到 172mm /min,则难以成形。且研究表明,在 300℃下,随着拉深速度的增加,AZ61、AZ31、M1 镁合金的极限拉深比成线性减小。
(2)模具结构 由模具间隙、凸凹模圆角半径、模具结构,拉深件形状等。在成形过程中,镁合金板材的成形效果和成形质量很大程度上受模具间隙的影响,目前,对于镁合金拉深件的成形主要采用较大的模具间隙。
(3)润滑条件 冲压工艺主要利用润滑剂来减小板材与凹模和压边圈之间的摩擦力,润滑方式对镁合金板材的拉深性能有很大的影响。目前,因镁合金的拉深工艺一般为热拉深,通常,拉深成形温度为 150~350℃范围内,可采用的润滑剂有二硫化钼、石墨、高温油脂等,也可选用塑料薄膜或玻璃纤维等代替润滑剂,提高拉深件的表面质量。有关手机外壳温成形的研究表明,在高温成形时,采用二硫化钼为润滑剂,成形效果较好。有关于肥皂、硅油和水基石墨三种不同的润滑方式对拉深性能影响的研究表明,采用肥皂做润滑剂,润滑效果较佳。也研究表明,在 150 ~400℃下进行成形时,动物油的润滑效果较佳。
(4)压边力的影响 压边力为冲压工艺的最重要的参数之一。在冲压成形过程中,施加压边的可以有效地防止坯料凸缘发生起皱现象。压边力过小,拉深件凸缘部位将会产生起皱;压边力过大,将拉深件凸缘压得过紧,板材的流动困难,容易产生拉裂缺陷。在拉深的开始阶段,凸缘起皱的趋势较强,应该采用较大的大压边力,随拉深的进行,起皱的趋势减弱,应该相应递小压边力,故冲压工艺中理想的压边力应该是变压边力。有关研究表明,对于方盒件的拉深形成,随着凸模行程而增加,最佳变压边力的加载曲线应该是 V 字型曲线。
(5)成形温度的影响 在高温下,镁合金的内能增加,非基面滑移系将被激活,其塑性成形能力得到提高,从而提高了镁合金的拉深性能。有关研究表明,在 50℃下,厚度为1mm 的 AZ31 镁合金板材,就有能实现低拉深件的冲压成形,其拉深比达到 1.5;在 200 ~250℃时,最大拉深比可达 2.5。王忠堂等对厚度为 1mm 的 AZ31 板材的拉深性能进行了研究[61],试研究表明:当坯料在 300 ~350℃内,模具温度控制在 170 ~210℃内时,镁合金板材的极限拉深比可达到 2.20;当温度高于 400℃或低于 200℃时,镁合金板材的拉深性能都会变差。有关 AZ31 镁合金板材手机壳冲压工艺的研究表明,凹模温度控制在 250 ~300℃、凸模温度控制在120 ~150℃时,拉深性能最好。张坤等有关 AZ31 镁合金板材采用液态的 PTFE进行润滑的研究表明[63],在 140℃下进行成形时,其 LDR 值有明显的提高,可超过 2.0;在 170℃进行成形时,其 LDR 值可达 2.4。有对 AZ31 镁合金方盒件温热拉延进行了研究[64]。研究证明:厚度为 0.5mm 的 AZ31 镁合金板材最佳成形温度是 200℃,并提出镁合金的最佳成形温度与板厚和拉延件形状密切的关系。同时有研究发现,对于 AZ31 镁合金,杯形件采用差温拉延工艺时,板材的 LDR 可达 2.1;若采用变压边力工艺时,板材的 LDR 可达 2.14;在板材温度为 400℃时,采用变压边力和差温拉延两种技术相结合的工艺,有效地控制压边圈与凹模的温度,并用冷却系统来冷却冲头。