冲压材料本构模型及模型参数的准确性是仿真模拟的前提。先进高强度钢、铝镁合金等高性能材料目前已得到广泛应用,其特殊强化机制导致其工艺特性、成形规律与传统钢板存在很大区别,因此在实际应用中遇到成形性能和回弹控制等多方面的问题。高强度钢板内部组织与传统钢板相比发生明显变化, 高强度钢在循环加载条件下具有更强的包辛格效应,并伴随相变的发生。因此,传统钢材的本构关系已不能适用于先进高强度钢板。 针对高强度钢板、铝镁合金板等先进材料,必须对成形极限曲线、变弹性模量、反向加载性能、材料变硬化指数和变各向异性参数进行系统研究,提出考虑相变效应的材料本构模型以及本构关系参数的获取方法,并考虑宏观、细观和微观组织体系,建立针对先进材料的多尺度耦合仿真算法,获得高可靠性计算结果。建立拉裂、起皱、回弹及焊缝失效的评价标准,提高成形缺陷的预测精度。 随着先进高强度钢、铝镁合金的广泛应用,热成形工艺的应用范围也在日益扩大。热成形过程中, 金属板材在高温和变形的共同作用下,板材微观组织产生明显变化,从而引起板料宏观力学性能产生变化,最终影响板料塑性变形过程。传统金属板材本构关系局限于金属宏观塑性流动行为,不能准确反映出热成形中复杂组织演变过程及材料真实力学行为。因此,需要建立变形、传热和组织演化的耦合本构关系模型以真实反映板料在热成形过程力学行为。美国俄亥俄州立大学 PALANISWAMY 等[1]采用有限元技术模拟镁合金在高温条件下的成形过程,同时指出模拟精度的提高需要更加适合于镁合金的材料屈服准则、处理高应变率和高温度场以及由于粘性效应引起应变软化情形的新型材料本构模型。
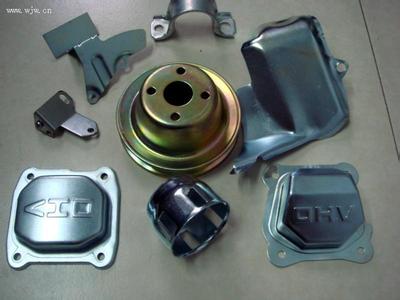
仿真用基础参数的获取包括板料的弹塑性本构特性参数、板料与模具间的接触摩擦特性参数、拉延筋特性参数等。目前,这些参数大量地来源于设计手册或材料供应商提供的数据。但由于大量数据是若干年前用相对落后的手段和装备获得的,而且现在新材料大量涌现,各种材料的成分和特性波动也较大,单靠设计手册中的数据已远不能满足需求。传统试验方法是采用标准试件承受某一特定载荷以满足特定的应力应变关系,如均匀的应力应变关系,然后用解析法分析参数和测试量之间的关系来标定待测量。显然要满足均匀应力应变关系等某些特定约束条件在实际操作中有很大困难。特别是当材料涉及大应变、非均匀变形或各向异性时,传统材料试验结果的误差较大,不能完全真实地反映材料的行为特性。然而在金属板材冲压过程中,冲压材料往往处于上述大应变及各向异性的情况下,因此采用以传统的标准试验方法获得的力学性能参数进行金属板材冲压过程计算机仿真时,所带来的误差可能使仿真在某种程度上失去意义。 基于样本试验与仿真的反求技术是一种新的板料特性参数获取技术,该技术与相应的冲压工艺综合试验装置配合使用,通过设计一组样本试验,在冲压工艺综合试验装置上,先获取给定板料在给定外载作用下的变形特性,再采用仿真方法获取对应的变形特性,并通过使仿真结果与试验结果不断逼近来反求与仿真算法匹配的真实板料特性参数,包括弹塑性变形参数和摩擦特性参数等。这一技术能及时反映材料特性参数由于成份波动等原因引起的变化,可从本质上提高仿真计算的可靠性。